Casting Simulation
Cast-Designer CPI (Casting Process Insight) è un potente strumento che definisce in dettaglio le informazioni sul riempimento, la solidificazione e lo scambio termico del getto da simulare, utilizzando la tecnologia FEM. CPI è stato progettato specificatamente per definire getti, stampi e processi produttivi in modo semplice se confrontato con la simulazione numerica tradizionale.
Con Cast-Designer CPI, il progettista può individuare posizioni potenziali dove possono sorgere problemi di riempimento o solidificazione per un dato sistema di pozzetti e di alimentazione. Non bisogna essere esperti di simulazione per usare CPI. CPI è notevolmente veloce e il tempo richiesto per valutare il progetto di uno stampo è ridotto. Quindi CPI può essere usato da chi produce, da chi crea lo stampo, o dal progettista del getto per ridurre il tempo di sviluppo e le modifiche allo stampo.
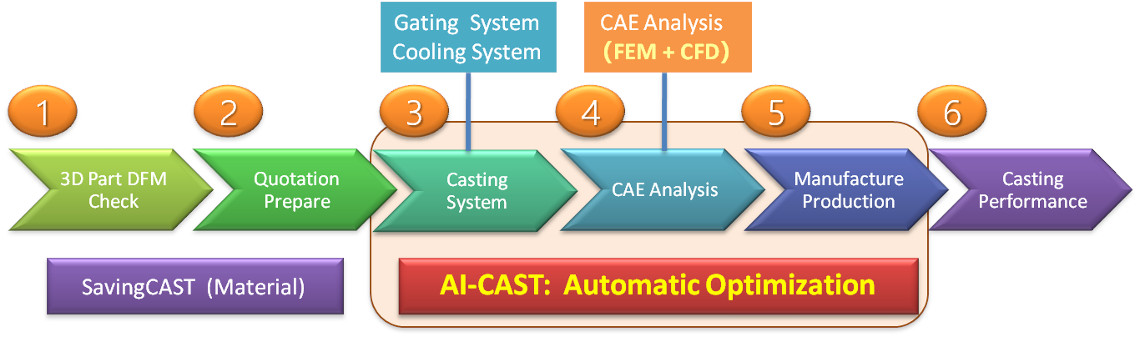
BENEFICI PER L’UTILIZZATORE
CPI è l’unico strumento veramente pratico sul mercato che aiuta il progettista e l’ingegnere a prendere decisioni veloci su come realizzare la parte e lo stampo per ottimizzare la produzione.
- Basata sulla più recente tecnologia FEM.
- Dispone di un potente motore per creare mesh di alta qualità da qualsiasi geometria CAD.
- Utilizza una tecnologia innovativa e molto accurata se confrontata col metodo tradizionale.
- Fornisce risultati in meno di un’ora partendo dalla geometria CAD.
- CAD integrato, strumenti di progettazione e analisi sono gestiti in un unico ambiente, la preparazione dell’analisi di un modello richiede pochi click e pochi minuti.
- E’ facile da usare ed ha una curva di apprendimento rapida.
IL MIGLIORE DELLA CATEGORIA
L’unicità di CPI è data dall’integrazione delle funzioni di progettazione di Cast-Designer e dalla velocità nell’ottenere risultati di analisi a qualsiasi stadio della progettazione dello stampo o della parte. Per esempio, nella fase di design concettuale dello stampo possono esistere numerose scelte alternative, uno strumento veloce è importante per valutarle e rimuovere quelle non valide. Quindi, in questa fase, la simulazione numerica tradizionale non è praticamente utilizzabile.
ORIGINAL DESIGN
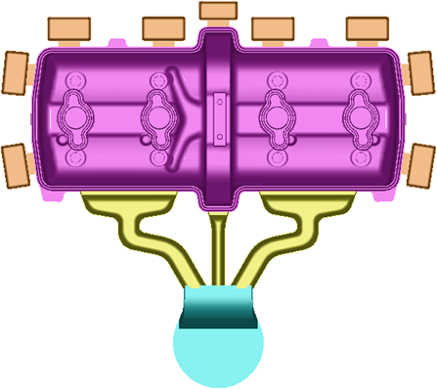
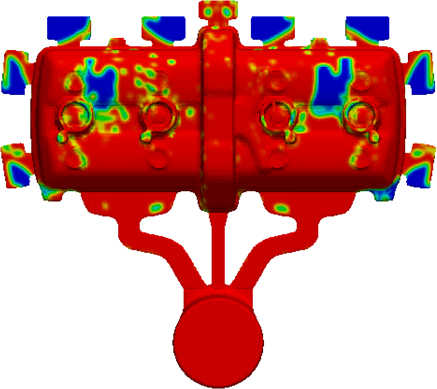
Air Entrapment in filling
In Cast-Designer si possono valutare numerose alternative progettuali e validarle nella simulazione CPI, per scegliere poi la migliore soluzione da produrre.
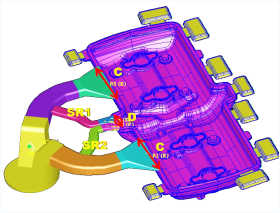
OPTIMIZED DESIGN
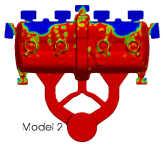
With Optional Sub-runner
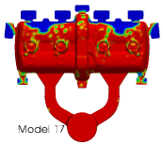
W/O Optional Sub-runner
Mesh potente per Parti ed Assiemi
Per lungo tempo l’operazione di mesh di parti ed assiemi è stata una delle più complesse per i software FEM, ora Cast-Designer la rende semplice e facile. Dopo oltre 20 anni di studi, numerose innovazioni e tecnologie esclusive rendono il processo di mesh in Cast-Designer facile, robusto, accurato e flessibile.
- Mesh 3D completamente automatica per generare mesh easedriche, senza necessità di una approfondita conoscenza CAE.
- Generazione della mesh velocissima e robusta, flessibilità nel controllo della dimensione in diverse direzioni.
- Preview in tempo reale della mesh risultante.
- Potente funzione “Group” per ristrutturare gli oggetti CAD, in modo da ricombinare o estrarre oggetti da component CAD esistenti. Con la possibilità di operazioni Booleane a livello di mesh, il motore della mesh si prende cura dei problemi di modellazione, come intersezioni a livello CAD, sovrapposizioni, fori o superfici danneggiate nel modello originale.
- I dati di partenza possono essere CAD o mesh superficiali ( STL ) o entrambi i tipi.
- Riparazione automatica dei difetti CAD come intersezioni, gap, fori o superfici danneggiate.
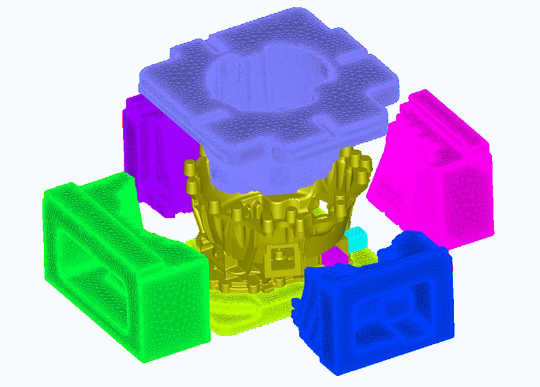
Full mould of aluminum wheel in LPDC
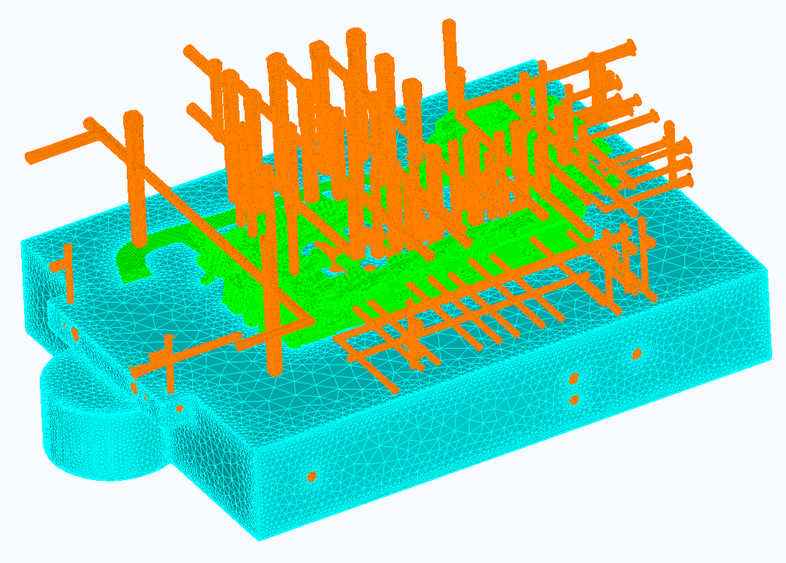
Full mould with cooling Channels in HPDC
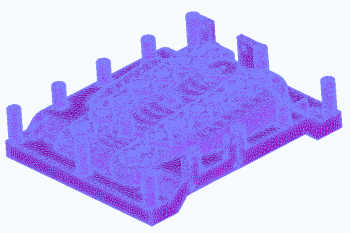
Top Die: 721,320 elements, 195,099 nodes (Tetrahedron)
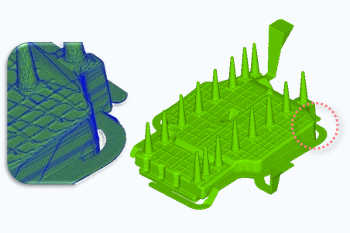
Casting Part: 436,679 elements, 604,052 nodes (Hexahedron)
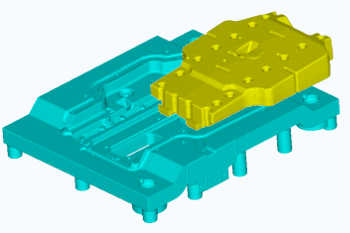
Sand Core: 776,328 elements, 203,632 nodes (Tetrahedron)
Bottom Die: 976,940 elements, 259,331 nodes (Tetrahedron)
Tecnologie innovative presenti in Cast-Designer
- Tecnologia “coarse mesh” per catturare dettagli e mantenere le pareti a spessore sottile con un numero di elementi ridotto
- Opzione “Automatic layer” per garantire un corretto funzionamento nel processo di riempimento
- Tecnologia di mesh locale con diverse densità, senza alcuna limitazione
- “Advance node smoothing” e “mapping technology” per mantenere una elevate qualità della mesh con una ottima descrizione della geometria
- Funzione “Mark point” per assicurare la qualità della mesh in punti prestabiliti
- Funzione “Catch up fine feature” per migliorare la qualità della mesh per geometrie minute in un numero molto ridotto di elementi
- Potentissima funzione di mesh di assieme. Supporta elementi di mesh misti in modo completamente automatico, è una tecnologia unica oggi sul mercato, le diverse mesh generate condividono gli stessi nodi per assicurare un corretto scambio termico
- Generazione di mesh superficiale con possibilità di remeshing per scopi particolari
- Potente funzione di generazione del guscio per la microfusione
- Salvataggio dei parametri della mesh con possibilità di riutilizzo in qualsiasi momento
- Supporta tutte le tipologie di processo produttivo
Velocità di simulazione per un tipico caso di pressofusione
- ~30 minuti per la generazione del sistema di alimentazione e dei pozzetti.
- ~10 minuti per la preparazione del modello per l’analisi.
- Da 1 a 1.5 ore per l’analisi termica e di riempimento.
- ~30 minuti per la creazione di un rapporto sui risultati.
Da 4 a 5 diverse soluzioni progettuali possono essere valutate in una giornata!
ANALISI DELLO STAMPO COMPLETO
L’operazione di mesh di assieme dello stampo completo viene effettuato semplicemente ed in Cast-Designer è possibile premendo un solo tasto. Vi sono molte innovazioni tecnologiche che lo rendono possibile. Una di queste è la tecnologia di remeshing delle diverse interfacce di contatto.
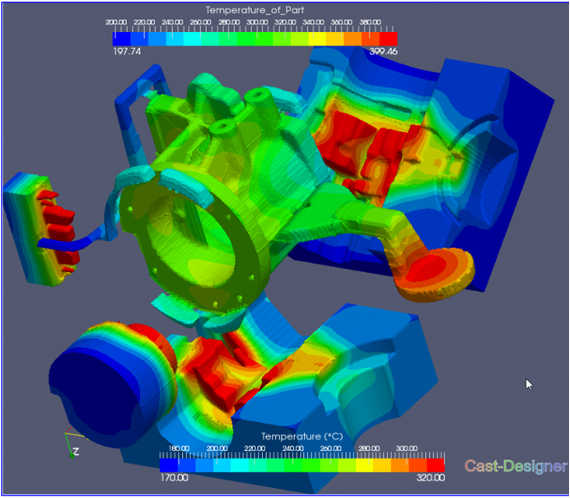
Casting and mould temperature of the casting process
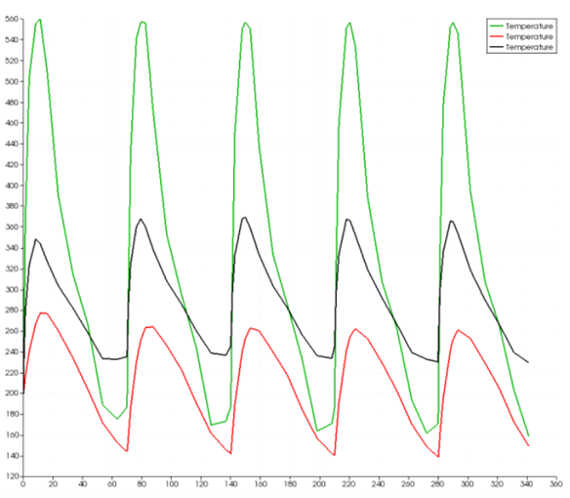
Cycling simulation to achieve the thermal balance
Il risultato della mesh di assieme dà un ottimo rapporto tra il getto e l’intero stampo. Il getto ha117,336 nodi, lo stampo fisso 44,993 e quello mobile 55,997, più quelli degli altri inserti, il rapporto globale effettivo è del 38,2%, davvero un ottimo risultato.
L’analisi dello stampo completo può essere usato per:
- Una analisi più accurata della temperatura. Solitamente è necessario anche nel processo di fusione per gravità in stampo permanente dove il tempo di riempimento è più lungo e lo spessore dello stampo ha un ruolo importante nel trasferimento termico.
- L’analisi del ciclo dello stampo per determinare la distribuzione di temperature stabile durante il ciclo di produzione.
- L’analisi termica dello stampo per determinarne il ciclo di vita.
- L’analisi di stress considerando lo stampo completo.
- L’analisi dettagliata del sistema di raffreddamento.
Database dei Materiali
Cast-Designer è dotato di un database dei materiali standard. Questo contiene oltre 400 tipi di materiali diversi. Ogni materiale è disponibile nel database e può essere selezionato in funzione del nome, oppure ricercato per famiglia o composizione chimica. Inoltre il database è facilmente personalizzabile aggiungendo nuovi materiali o modificando i valori di quelli esistenti.
Processi di fusione e moduli avanzati
- Thixo-casting
- Formatura semi-solida e forgiatura liquida.
- Squeezing casting e local pin squeezing.
- Analisi della microstruttura per Al e Mg.